How Operators Benefit from Next-Gen Manufacturing Equipment
Brandon Glenn 05.20.2022
We’ve all noticed the many ‘help wanted’ ads throughout our communities, even within machine shops. But the truth is, even before COVID-19 disrupted the manufacturing industry, U.S. manufacturers were struggling to fill open positions.
I ran across a stat reported by Deloitte and the Manufacturing Institute stating half of the 2.4 million manufacturing jobs that were open in 2018 could remain unfilled through 2028. Three years and one pandemic later, those predictions feel like they are close to spot on.
It begs the question, why?
The overall perception of manufacturing
We hear it all the time in conversations with our colleagues and shop owners around the country, part of the problem is finding people with the right skill sets and manufacturing background. But some would argue, especially those from our Okuma Machine Tool Academy, that it’s more about how manufacturing jobs are viewed by the public. In a fast-paced, high-technology-driven society, manufacturing seems out-of-date, unexciting, and even a little dirty. Of course, for all of us in this industry, we know this couldn’t be further from the truth – and we must work to change this overall perception for the next generation.
“In a world ruled by technology, manufacturing seems old school. Of course, the reality is just the opposite.”
- Manufacturing Business Technology, Feb. 2022
Today’s high-tech manufacturing equipment are the horses that drive production. Could it also be that, with the right technologies, interfaces, support, and messaging, these same machines can also help attract and retain A-list talent? Okuma believes the answer is yes!
New equipment shattering old perceptions
As previously stated, manufacturing may have an image problem. Unfortunately, this directly affects job shops’ ability to recruit and retain quality talent. The traditional view of manufacturing – as being non-skilled, manual, repetitive, and marginally challenging – is turning away the next generation of operators. But with the heightened inclusion of automation and robotic systems, cloud-enabled digital technologies supported by the Industrial Internet of Things (IIoT), environmental-friendly design builds, and even social media influencers changing the narrative, the machining industry is primed to attract top talent.
The new capabilities are reflected in modern machine tools and supporting equipment that not only enhance productivity, consistency, and quality, but also help stimulate, protect, and reward those who operate them. From lathes and machining centers to grinders and lasers, today’s machine tools are designed to provide key benefits to the employee as well as the employer.
Controls that drive better employee engagement
More and more, equipment control panels are beginning to take on the look and feel of fast-paced video games. Highly interactive and data-rich controls like those shown below keep the operator more informed and engaged. In doing so, this interactivity recasts their daily role as a problem-solving data analyst actively seeking to improve the machining process and the shop’s profitability.
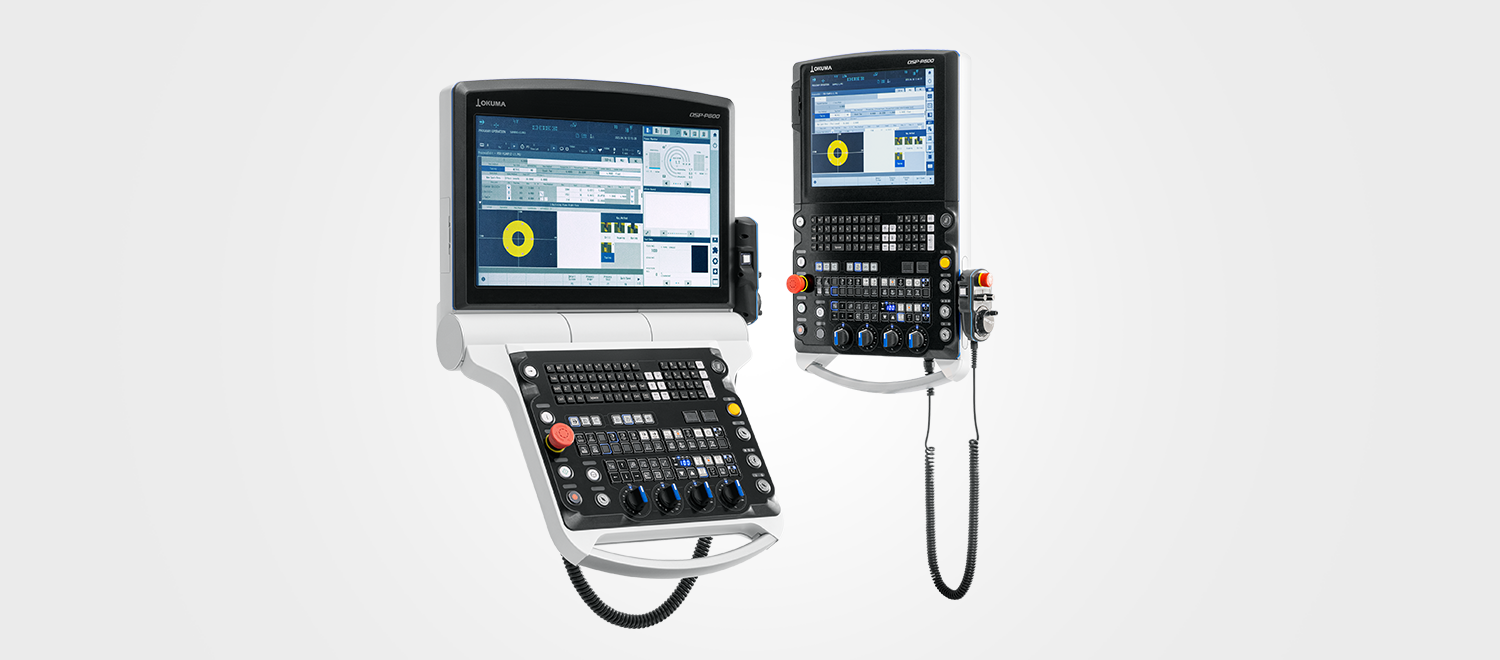
Control interfaces like those found in the Okuma’s OSP suite are also highly configurable. For example—our new, next-generation OSP-P500 control has two sleek, user-friendly configurations with features that can be set up differently. Each user can customize the operation panel, adding helpful applications, shortcuts, and common tasks to suit his or her preference and skill level. A variety of available OSP apps also enables operators to add customized on-screen shortcuts, user settings, maintenance reminders, and displays. Beyond improving operator performance, this helps cultivate a sense of ownership in the machine, the cutting process, and the company.
Reducing physical stress
Even in job shop environments where injury rates are relatively low, the physical demands of the job, if done improperly, could contribute to chronic pain, absenteeism, and even employee turnover. By investing in equipment that is more ergonomically designed, employers can reduce some of these effects.
Okuma’s GENOS series machining center is designed with a specific focus on operator ergonomics. For example, the automatic tool changer (ATC) access window is located on the front side of the machine, allowing operators to change tools safely and easily. Compared to other models that require loading tools through the spindle, the GENOS’s ATC access window significantly reduces repetitive motion and stress to the operator’s lower back, neck, and shoulders.
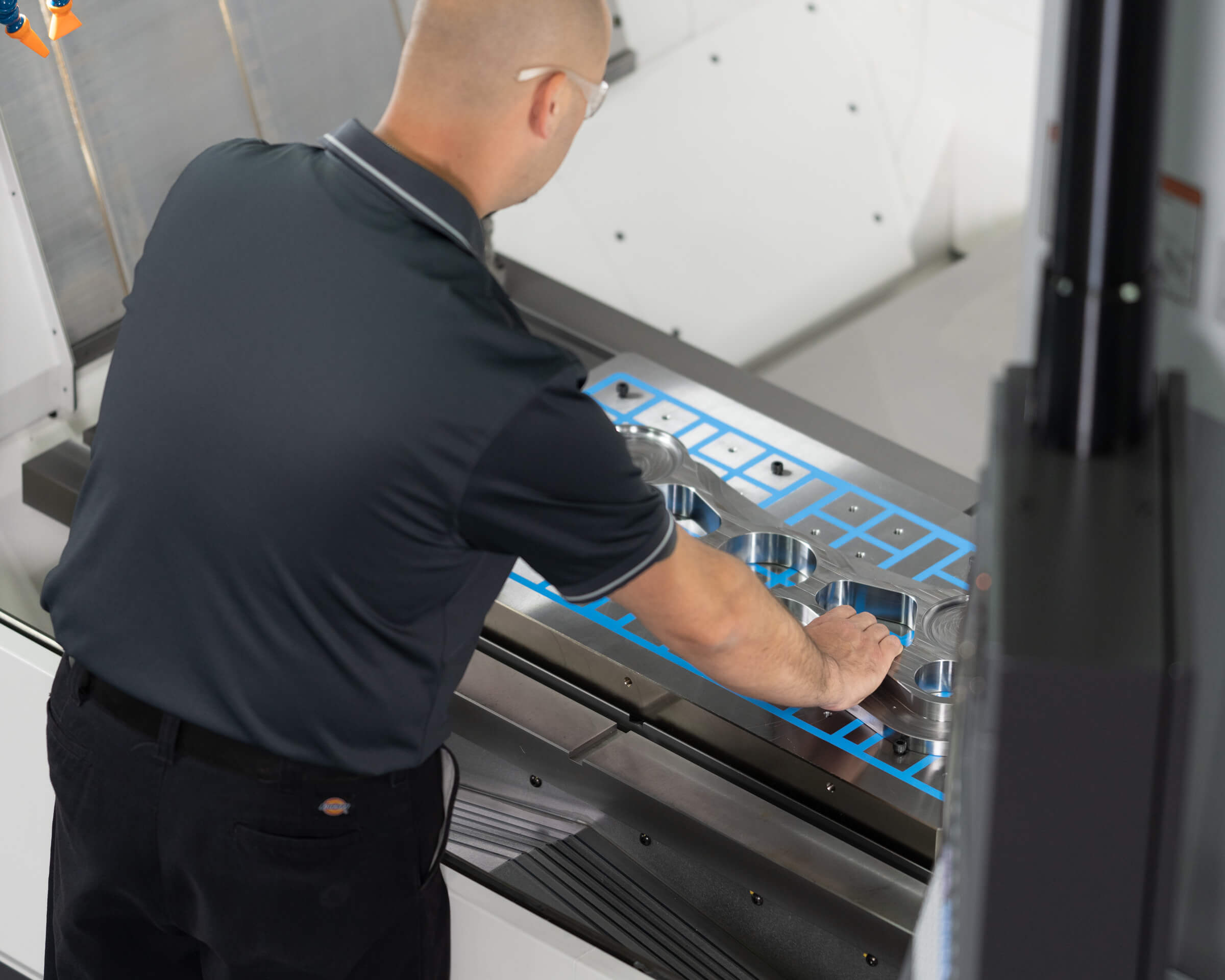
Other Okuma machine tools offer articulating control panels that swivel or swing in and out to provide better accessibility. We’ve also invested significant research and resources in developing machines with greater mass and technologies to dampen machine vibrations, which has enabled manufacturers to effectively reduce noise levels in a shop environment. Customizable LED lighting kits provide better illumination of the work area and reduce eye strain.
Ergonomic improvements like these can also have a positive effect on how employees view their jobs, especially when employees notice the company is putting forth its best efforts to ensure their health, safety, and comfort.
Touching on new values that matter
Younger generations look for ways to make their place of work have meaning, and how a company addresses environmental sustainability and corporate responsibility are qualities they look for when searching for their next career.
Through innovation and our passion for continuous improvement, Okuma continues to evolve our products to minimize environmental impact, and we invest in manufacturing technologies that are environmentally friendly. Our newest ECO suite plus energy-saving control application is one way we are accomplishing this goal.
With this next-gen system, operators have the power to monitor, manage, and reduce energy-heavy operations like running auxiliary pumps and other peripheral equipment – giving them a sense of responsibility and empowerment. Features of ECO suite include:
- ECO Idling Stop: Monitors the cooling status of the milling and turning spindles, and automatically turns off the coolers for these spindles when spindle temperature is stable
- ECO Power Monitor: With power consumption shown for spindles, feed axes, and peripheral equipment right on the machine tool’s display, you can see exactly how much energy is being saved
- ECO Hydraulics (optional): Utilizing SERVO control technology, this feature actively monitors the demand of the hydraulics to activate the pump only when necessary to maintain pressures as called
- ECO Operation (optional): Peripheral equipment will only run when needed and will automatically stop after cutting is finished
Manufacturing equipment must do more than manufacture
Employees, both current and future, have made it clear they want to work and are willing to work hard, provided they feel meaningfully engaged and know that the business is committed to their all-encompassing personal and professional well-being. Obviously, creating a positive working environment and corporate culture requires more than a better machine tool. But advanced manufacturing equipment – which stimulates worker engagement, provides ownership of the process, and is thoughtfully and ergonomically designed – has an important role to play.
To learn more about how Okuma’s wide breadth of machine tools, automation systems, and partner technologies can begin to make a difference for your employees and on your shop floor, contact your local distributor.
We offer a variety of ways for you to stay informed about our events, and to receive general Okuma updates. Fill out the form below to let us know the type of information you'd like to receive.