Hand Scraping Sets the Foundation for CNC Machining Accuracy and Long-Term Stability
10.03.2013
Executive Summary
Hand scraping is a practice that has lost its luster for many CNC machine tool builders. Because of the associated costs in time and maintaining skilled labor, it’s an art that has largely been abandoned. At Okuma however, hand scraping is meticulously performed on every machine we build. That’s because there’s no substitute for hand scraping when it comes to maintaining high levels of CNC machining accuracy and sustaining a long, stable and productive life for your machine.
Every Okuma is hand scraped on each mating surface – involving six or more of the machine’s components. The craftsmen who perform hand scraping are carefully trained, and tap into their experienced, intuitive sense of how to fine-tune the unique characteristics of each individual machine. Why go to all this trouble? Because there’s no better way to ensure that tight tolerances are maintained consistently, and that this level of CNC machining performance will be sustained for years to come. As for lifetime cost of ownership – highly productive machines that last a long time always yield the lowest cost-per-part.
DOWNLOAD THIS WHITE PAPER
This white paper is also available as a free downloadable PDF. Or, you can continue reading it below.
THE ESSENTIAL OBJECTIVES OF HAND SCRAPING
Hand scraping sets the foundation for productive CNC machining. It is performed with the following objectives in mind:
- Accuracy: Scraping is done to align components within millionths of an inch, allowing for consistently-held, tight tolerances.
- Flatness: Eight to ten contact points per square inch are created to prevent rocking, add balance when tightening, and to allow for true flatness in parts.
- Oil Pockets: Some machine surfaces have oil injected onto them. Hand scraping allows for creation of oil pockets, which holds oil on the surface and allows for gliding motion. Without oil pockets, two flat surfaces will stick together.
- Appearance: The finishing touch of scraping is aesthetic. Once accuracy, flatness, and oil pockets are handled, parts are “design scraped” to achieve an attractive textured finish.
FLAT MACHINE SURFACES DO NOT CREATE CONSISTENT PARTS
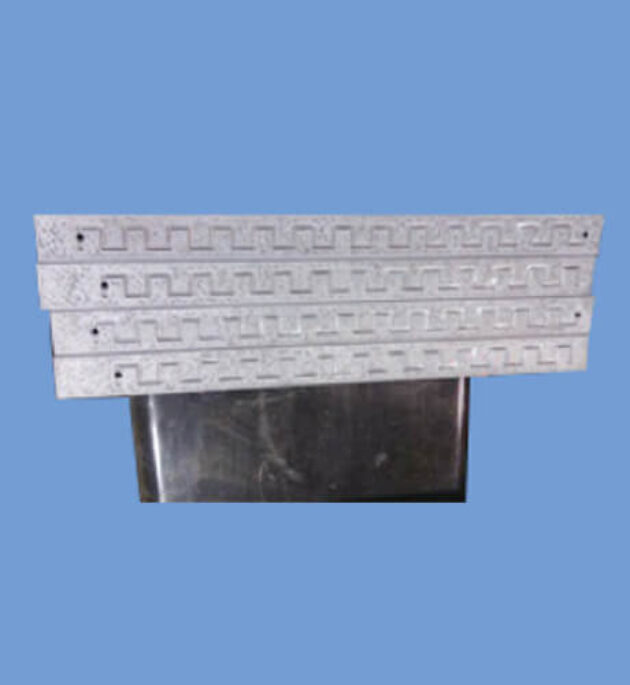
Hand scraping introduces carefully placed high and low spots on the mating surfaces of the CNC machine (see Figure 1). While it’s natural instinct to believe that flat surfaces would be better for machining accuracy, this is, in fact, not true. Two flat surfaces in contact on the machine will stick, creating inconsistent machining characteristics. Tight tolerances can only be achieved by adding high and low spots that hold oil and allow for gliding, rather than sticking. Introducing more contact points via the high and low spots also allows for balance and therefore perfect mating. With flat surfaces there is only one contact point, which creates a state of imbalance.
For moving parts, introduction of high and low points allows the two surfaces to glide together without sticking. For bolted parts, hand scraping creates a tighter fit, which is less likely to separate as a result of the material expansion, contraction and flexing that occurs during CNC machining processes.
THE HUMAN TOUCH
For all CNC machine tool builders, machine components are fundamentally comprised of castings. However molding these castings is not always a consistently repeatable process. Okuma recognizes this and utilizes hand scraping to ensure that the machine tool starts out with a solid, rigid foundation. There are uncontrollable process variables in casting such as slight changes in base materials, mold release agents, temperature and environmental conditions that cause each component to have unique characteristics. And, while metal behaves in similar ways from one casting to the next, once it’s released from a constrained position it can move and flex in unpredictable ways. Hand scraping corrects fluctuations arising from these variables.
Hypothetically, if a mechanical process were used to perform hand scraping, it would necessarily be based on predictable outcomes. That’s the nature of machining processes. However, due to the variables described above, each component must be handled with consideration for its unique characteristics. This can only be done by experienced artisans who can see, touch and feel where, and how, the scraping must be applied. Okuma’s hand scraping professionals utilize several specialized tools in a variety of motions. Hand pushing, “body power strokes,” and curved scraping are performed as needed to maximize the efficiency of the machine tool’s operation.
KEY MACHINE COMPONENTS
Hand scraping is performed on all components of Okuma machine tools that involve mating surfaces. This includes six (or more) of the machine’s components (See Figure 2):
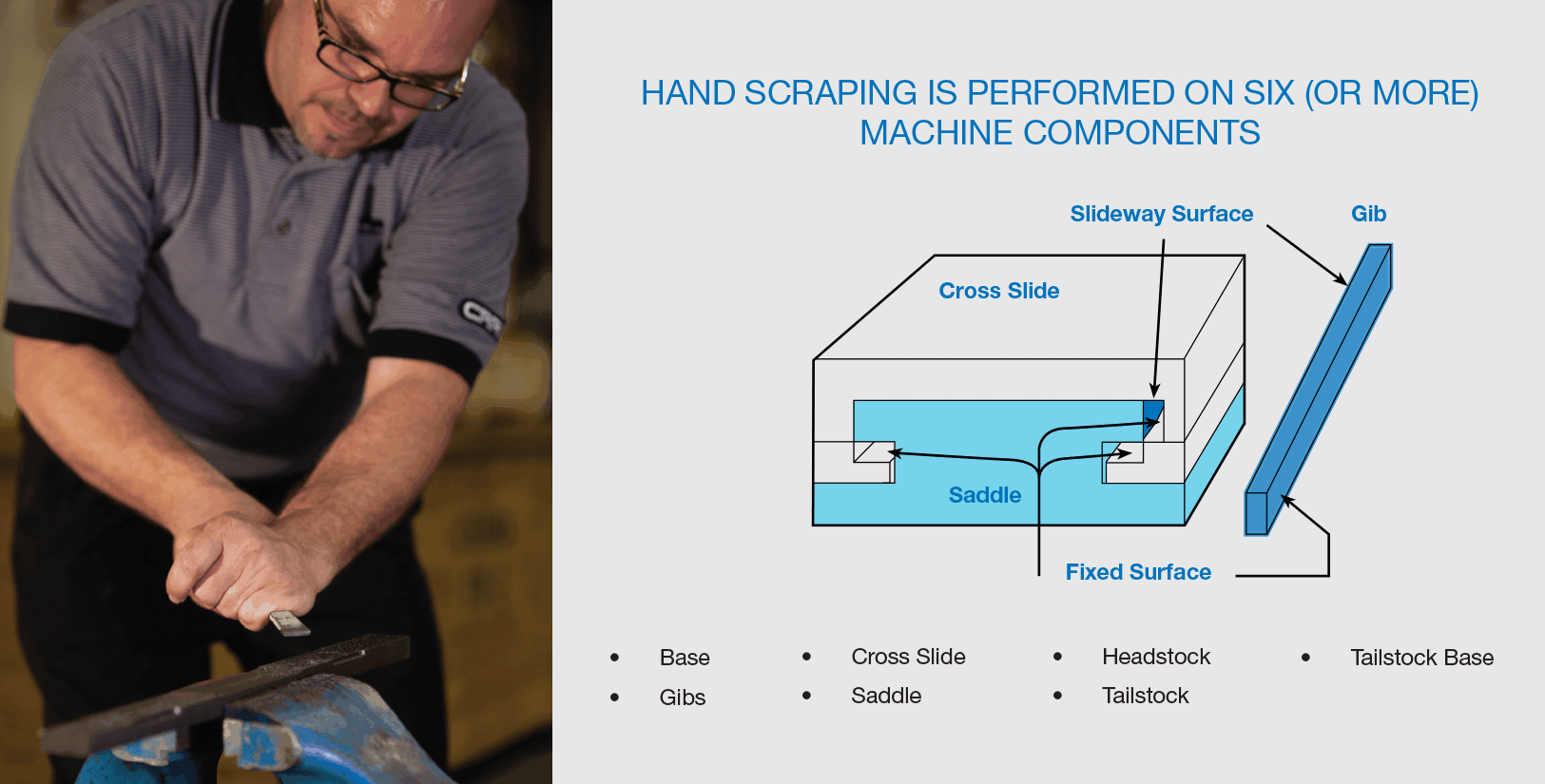
REDUCED COST OF OWNERSHIP
Clearly, hand scraping adds some cost to the machine building process. However, by fine-tuning the machine so that it operates in balanced harmony rather than creating wear and tear on itself and on parts, more, higher-quality parts are produced, and the machine lasts longer. Okuma does not embrace a “disposable parts, disposable machine” philosophy.
We do hand scraping because we know that lifetime cost of ownership and cost-per-part are reduced when you produce more, quality parts over a longer time frame.
LONG-TERM ACCURACY AND PRODUCTIVITY MAKE GOOD BUSINESS SENSE
Hand scraping is used on every machine built by Okuma because it is essential to creating a solid, efficient machine tool foundation. It combines art and science with the personal touch of skilled craftsmen. Hand scraping enables consistent high-accuracy and long-term performance, and makes good business sense for every CNC machine shop.
To learn more about hand scraping, check with your local Okuma Distributor, or visit the Okuma website at www.okuma.com.
To view hand scraping in action, check out our video: