Super-NURBS Cuts Curved Surfaces with Accuracy and Speed - Completing Parts on the Machine
11.03.2013
EXECUTIVE SUMMARY
When it comes to curved surfaces, smooth finishes are critical. Super-NURBS is a programming functionality for CNC machining that meets high-accuracy finish requirements while speeding up cycle times. The result is drastically reduced hand-finishing time to achieve high-quality parts quickly. By combining Okuma’s solid CNC machine tool foundation with the high processing speed of Okuma’s THINC®-OSP CNC Control, users can deliver parts out the door faster, with better finish quality and accuracy. Super-NURBS is excellent for machining parts with high-accuracy requirements such as those for mold & die and aerospace/defense.
DOWNLOAD THIS WHITE PAPER
This white paper is also available as a free downloadable PDF. Or, you can continue reading it below.
What is Super-NURBS?
The term “NURBS” is an acronym for Non-Uniform Rational Basis Spline. This was developed in the 1950s as a mathematical way to regenerate freeform curves and shapes such as car bodies and ship hulls. It became commonly used in most CAD software packages along with CAM systems and is part of industry standards like IGES and STEP files. Super-NURBS is Okuma’s proprietary technology for achieving NURBS functionality within a CNC machining environment. With Super-NURBS, the OSP control projects a predetermined tolerance band that creates a spline considered to be the best fit for the job. This eliminates redundancies and allows for a faster and smoother tool path (see Figure 1). With less data to crunch, movements are sped up—while maintaining a high level of accuracy to generate high-quality surface finishes.
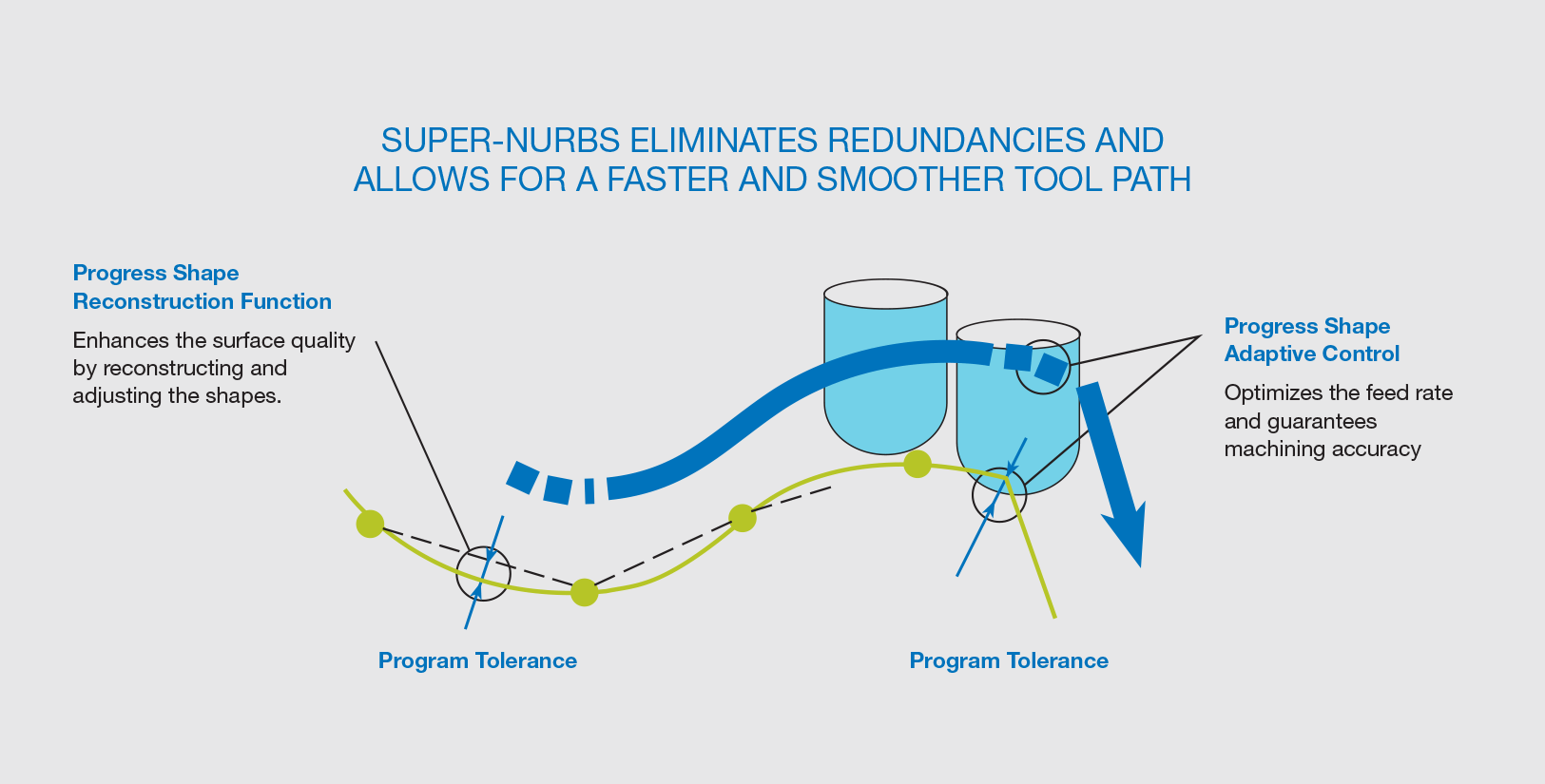
THE SUPER-NURBS DIFFERENCE
Super-NURBS is able to deliver the fastest speeds and highest quality finishes in the industry. This is due in part to its foundation in the mechatronics approach, Okuma’s blending of mechanical and electrical development to assure optimized communication between the machine and its control. Super-NURBS also delivers the following unique benefits:
- Faster Control Loops Speed: The feedback loop determines how quickly the CNC machine can “talk” to the encoder and servo units. With Super-NURBS, the machine is faster in telling the servo where to move, and in receiving confirmation of getting information, allowing for more ultra-high feedrates to be used. At times, this can involve “talking” to as many as five servos simultaneously. [Graphic: Video] [Caption: Super-NURBS completes a part that typically took 55 minutes in 30 minutes, while maintaining a highly accurate finish.]
- Digital-to-Digital: While controls are digital, many machine tools in the industry still use analog. This requires translation activity that slows down the CNC machining process. With Okuma machines outfitted with Super-NURBS, the control loops feed is digital-to-digital, which speeds up the communications process and therefore allows for faster machining. There is no need for a look-ahead within a Super-NURBS system because it’s inherently fast without it.
- Machine Build Quality: Okuma delivers the complete package of machine and control. The build quality of Okuma CNC machines enhances overall functionality, with features including: ribbed castings for strength, large base casting with three-point leveling, integrated ballscrew mounts to ensure rigidity, cantilevered column to reduce weight and resist bending, handscraped cast mating surfaces for superior flatness and contact, and a work area enclosed in sheet metal to eliminate hot chips and coolant from contacting castings, which minimizes thermal influences.
IMPACTS FOR THE CNC MACHINING ENVIRONMENT
With complex curvature shapes, a CAM system will output a series of X, Y and Z points (in a 3 axis example). It will create the curve using piecewise linear movements. Therefore, in order to generate a curve, it will actually utilize many small linear movements. When left in that form, as part of the feedback processing loop, the CNC control will attempt to drive to each individual point and ask for confirmation if it made it to its intended destination. The CNC machine may never reach it’s programmed speed because it can only crunch so much data before it has to start slowing down to maintain the feedback loop and keep the programmed accuracy. This is something machinists and programmers have no control over, the machine control makes the decision on how fast it can go while maintaining the point-to-point accuracy of the shape.
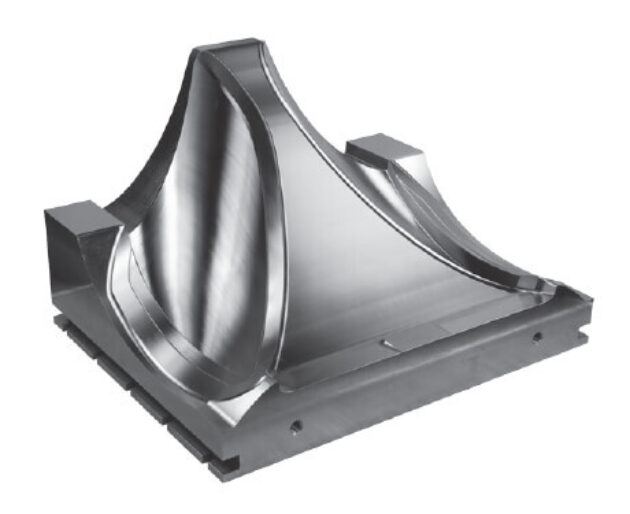
With Super-NURBS, the OSP control projects a tolerance band that is predetermined by the programmer through the series of points. Based on this, it will create a spline that is a “best fit” and may eliminate some of the points that are redundant to the spline path. This allows for a smoother tool path, and because we eliminate some of the points, the positioning feedback does not need to crunch as much data and can speed up the movements while still maintaining accuracy.
COMPLETING PARTS ON THE MACHINE
The result is controlled high speed and high-quality CNC machining. With faster roughing speeds and better surface finishes, hand-finishing is eliminated. Completing parts on the machine – this is possible with Super-NURBS.
LEARN MORE
For more information about Super-NURBS and the products on which it is available, check with your local Okuma Distributor, or contact us.